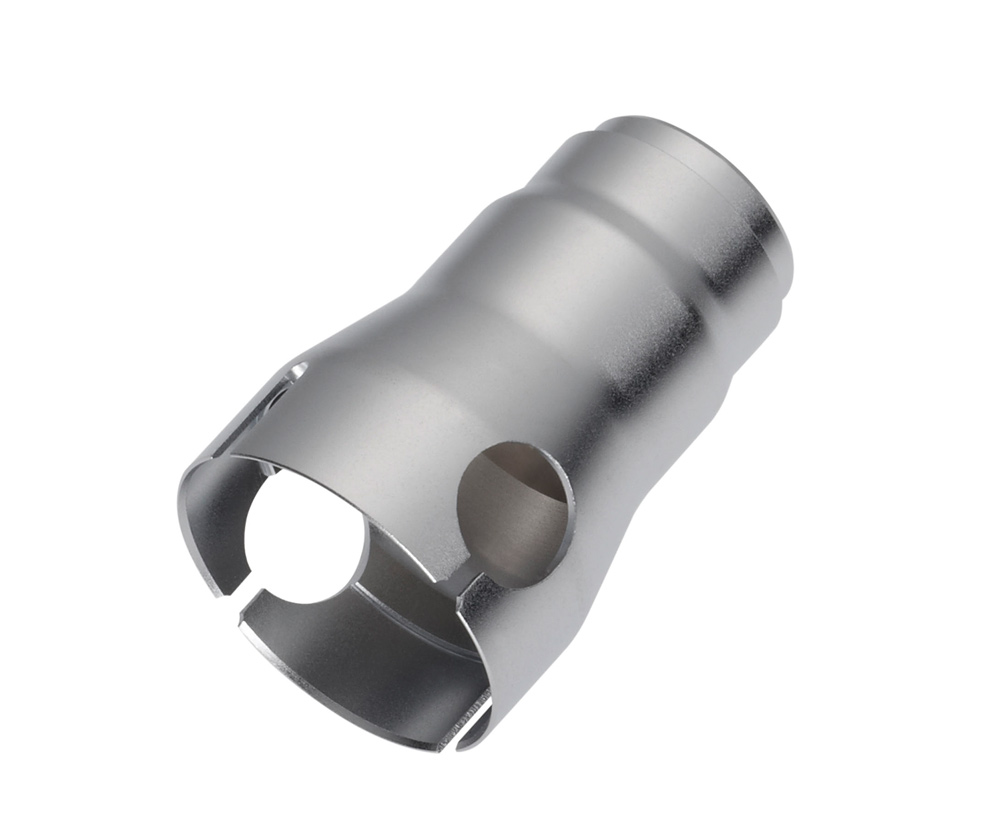
北京机械加工厂车床切削油雾润滑技术优点和装置
2024-04-11
北京精密机械加工厂常用的对刀方法:
一、采用寻边器、偏心棒和轴设定器等工具对刀法:
操作步骤与采用试切对刀法相似,只是将刀具换成寻边器或偏心棒。这是最常用的方法。效率高,能保证对刀精度。
机加工操作员使用寻边器时必须小心,让其钢球部位与工件轻微接触,同时被加工工件必须是导体,定位基准面有较好的表面粗糙度。z轴设定器一般用于转移对刀法。
二、转移对刀法:
加工一个工件常常需要用到不止一把刀,第二把刀的长度与第一把刀的装刀长度不一样,需要重新对零,但有时零点被加工掉,无法直接找回零点,或不容许破坏已加工好的表面,还有某些刀具或场合不好直接对刀,这时候可采用间接找零的方法。
1.对第一把刀
① 对第一把刀的时仍然先用试切法、塞尺法等。
② 把对刀器放在机床工作台平整台面上。
③ 手轮模式下,利用手摇移动工作台至适合位置,向下移动主轴,用刀的底端压对刀器的顶部,表盘指针转动,最好在一圈以内,记下此时轴设定器的示数并将相对坐标轴清零。
④ 确抬高主轴,取下第一把刀。
1.对第二把刀。
①加工师傅 装上第二把刀。
② 机械加工厂家操作人员在手轮模式下,向下移动主轴,用刀的底端压对刀器的顶部,表盘指针转动,指针指向与第一把刀相同的示数位置。
③ 记录此时轴相对坐标对应的数值。
④ 抬高主轴,移走对刀器。
⑤ 将原来第一把刀的G5*里的z1坐标数据加上数,得到一个新的坐标。
⑥ 这个新的坐标就是要找的第二把刀对应的工件原点的机床实际坐标,将它输人到第二把刀的G5*工作坐标中,这样,就设定好第二把刀的零点。其余刀与第二把刀的对刀方法相同。
三、试切对刀法:
这种方法简单方便,但会在工件表面留下切削痕迹, 且对刀精度较低。以对刀点(此处与工件坐标系原点重合)在工件表面中心位置为例采用双边对刀方式。
1. x,y向对刀。
① 将工件通过夹具装在工作台上,装夹时,工件的四个侧面都应留出对刀的位置。
② 启动主轴中速旋转,快速移动工作台和主轴,让刀具快速移动到靠近工件左侧有一定安全距离的位置,然后降低速度移动至接近工件左侧。
③ 靠近工件时改用微调操作(一般用0.01mm)来靠近,让刀具慢慢接近工件左侧,使刀具恰好接触到工件左侧表面(观察,听切削声音、看切痕、看切屑,只要出现一种情况即表示刀具接触到工件),再回退0.01mm。记下此时机床坐标系中显示的坐标值。
④ 沿z正方向退刀,至工件表面以上,用同样方法接近工件右侧,记下此时机床坐标系中显示的坐标值。
⑤ 据此可得工件坐标系原点在机床坐标系中坐标值。
⑥ 同理可测得工件坐标系原点在机床坐标系中的坐标值。
2.z向对刀。
① 将刀具快速移至工件上方。
② 启动主轴中速旋转,快速移动工作台和主轴,让刀具快速移动到靠近工件上表面有一定安全距离的位置,然后降低速度移动让刀具端面接近工件上表面。
③ 靠近工件时改用微调操作(一般用0.01mm)来靠近,让刀具端面慢慢接近工件表面,使刀具端面恰好碰到工件上表面,再将轴再抬高,记下此时机床坐标系中的z值,则工件坐标系原点W在机床坐标系中的坐标值。
3.将测得的x,y,z值输入到机床工件坐标系存储地址G5。
4.进入面板输入模式(MDI),输入“G5*”,按启动键(在自动模式下),运行G5*使其生效。
5.检验对刀是否正确。
四、塞尺、标准芯棒、块规对刀法:
这种方法与试切对刀法相似,只是对刀时主轴不转动,在刀具和工件之间加人塞尺(或标准芯棒、块规),以塞尺恰好不能自由抽动为准,注意计算坐标时这样应将塞尺的厚度减去。因为主轴不需要转动切削,这种方法不会在工件表面留下痕迹,但对刀精度也不够高。